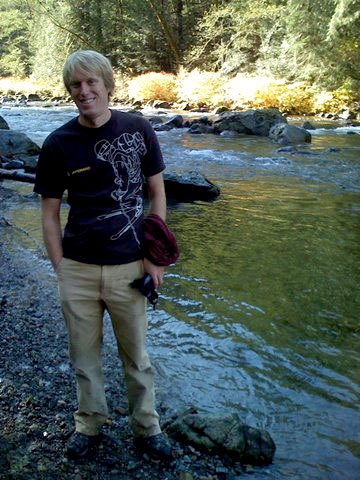
Designer Brent Zwiers of Feathered Friends, alongside the Skykomish River near Stevens Pass, Washington.
Outdoor enthusiast, husband, and jack-of-all-trades Brent Zwiers of Feathered Friends is one of the design minds behind the family-owned, Seattle manufacturer's handmade down sleeping bags and clothing.
Zwiers recently shared some of his gear designer experiences, skills, and secrets with Trailspace.
Q: What’s your official title?
A: This will probably be the hardest question because our company is so small that you have to wear so many hats. I guess if I had to make one up, I’d say the Director of Operations of Sourcing and what falls into that is design, materials overseeing, customer service, international sales, financial management, and a whole bunch of things.
Q: What does your business card say?
A: It doesn’t say anything, actually! It just has my name on it.
Q: How long have you worked for Feathered Friends?
A: I’ve been here about twelve years. I used to live in Minnesota, so I would come out in the winter and work part time and help out on the sales floor or do anything just not to be bored. Full time it’s been about eight or nine years.
Q: Is Seattle your hometown?
A: No, actually Iowa is my original state. I was born in northwest Iowa but I grew up in Pella, which is southeast of Des Moines about forty miles, a small town of 10,000 people.
Q: How did you find Feathered Friends?
A: I went to school in Minnesota and actually have a degree from St. Olaf College in French horn performance, believe it or not. I was pursuing music and needed a job to pay for that pursuit.
So I grew up with my family, my parents [were] both teachers, so every summer we would take off in the camper and go somewhere. By the time I graduated college, I had been in almost all fifty states, and so I knew stuff about the outdoors and had an attraction to it.
REI was opening their second flagship store, so I got a job there in the footwear department to help pay the bills. I started learning as much as I could and eventually found out about Feathered Friends as manufacturers of the world’s best down stuff. When I came out here [Seattle] every winter with my friend who was starting graduate school — we’re climbing partners — I started hanging out here and they asked if I wanted to work and I was like ‘sure,’ so that’s how it happened.
Q: Do you still play the French horn?
A: Only for Christmas when I go home to play with my mom in church. I still really enjoy it and I would love to have the time to do it.
Q: How did you get involved in the actual design part?
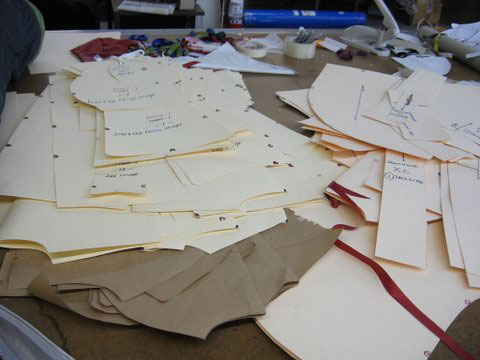
Design table with pattern pieces laid out.
A: Feathered Friends doesn’t have the payroll to have a dedicated designer or design team and we don’t have the dollars to outsource, so it’s more of when you get involved in sourcing and production, you start to learn how things go together, materials, and you combine it with your own personal experience in the outdoors and seeing from the marketplace what needs to be done, hearing back from the athletes who are out there using stuff.
And then you just kinda come up with some ideas and then you put those ideas together and come up with some new things. So it wasn’t like, ‘I’m going to be a designer’ it was that there was a need to be filled.
Q: What would you suggest to an aspiring gear designer?
A: I definitely wouldn’t suggest that you go to school for French horn performance! Maybe the root of it is creativity, so that would be helpful. I’m sure there are lots of traditional avenues, but the way I ended up doing this was certainly not traditional. I’m sure they would study design or architecture or engineering or something more applicable with technology and the sciences. But that’s purely guessing.
Q: What does a typical day or week entail?
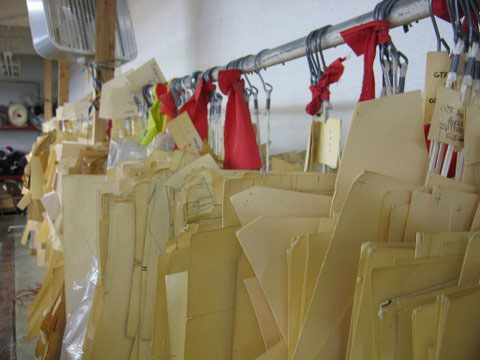
Down jacket patterns.
A: That’s the great thing about working here, that there’s not really a typical day or week. It makes you stay on your toes, stay fresh, keep you challenged. Some of the tasks that have to get done are financial management. How good were sales? What do we need to pay?
But for instance this week, I’m meeting with our Japanese distributor on Wednesday and our Korean distributor on Friday, doing this interview with you, getting ready for a sale that’s coming up, a staff meeting, coaching and training, rolling out new products, and working on a website redesign.
Q: How many bags have you made/designed?
A: I’d say that I’ve designed, start to finish, two or three and had a hand in changes we’ve made in our line in probably another dozen or so.
Q: What's your favorite piece you've designed?
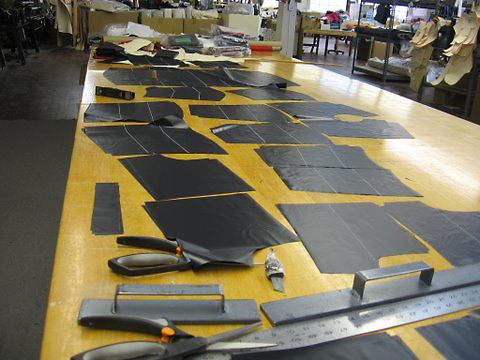
Cutting table with cut jacket pieces laid out.
A: By far, my favorite design was one that was the most challenging bag to design that we just rolled out last year called the Spoonbill. It’s an amazingly complex piece of engineering and it’s amazingly specialized in its application. It’s a two-person sleeping bag designed for alpine climbers.
Usually alpine climbers save weight on the routes by taking a single sleeping bag. We knew this was going on and thought we could engineer something to give people more comfort without carrying much more weight than a single bag. So it was happily named the Spoonbill.
It has a top and a floor, two collars, two individual hoods. The complexity of putting that together proved to be really challenging. The bag weighs under three pounds.
Q: What's the coolest detail you've designed that the average person probably wouldn't notice?
A: I think the coolest thing has more to do with materials than it does about the construction aspect of the design. A sleeping bag for the most part is reasonably straightforward. Other people are doing nichey marketing things out there, like a stretch panel here, a vertical this, extra little doodad there, and I’m sure they serve some function for the most part.
So to me the most exciting part of the design is about materials. And when we go and meet with material suppliers, fabric is not just fabric. The innovation is just amazing from year to year.
Q: Have you ever come up with a bag feature that seemed like a great idea on paper, but didn't work out in practice?
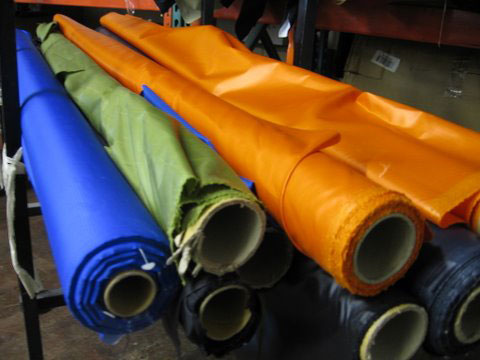
Mix of Feathered Friends fabric.
A: That’s kinda a stumper. One thing that we did that flopped was a design for the Backpacker Green Challenge for who could make the greenest, most earth-friendly sleeping bag. And we actually won the competition with a bag called the Blue Heron (men's) and Green Heron (women's)!
We used recycled fabrics, obviously manufactured here in the U.S. Our store is only six block from our factory, so we are able to walk the products up. No waste regarding carbon footprint…and I think we sold two of them. It was a great bag, it worked really well, and it just didn’t sell.
[Editor's note: Feathered Friends can still make a Blue or Green Heron bag on request.]
Q: Are your bags made to order?
A: Pretty much all our bags are made to order. We try to stay ahead of the curve a little bit so the wait time isn’t so long, but we’re not sitting on thousands of completed pieces.
Q: Is there a personal favorite feature that you try to incorporate in most designs?
A: For down in particular, we always try to use a water-resistant fabric of some sort. That’s the biggest hurdle a customer has with down, that they think if their down gets wet they are going to die or it will ruin their trip.
To some extent, that’s not an unreasonable fear. So we always push the envelope in terms of fabric. Back in the day when Gore was coming out, we were the first to put it in our sleeping bags.
Q: How does Feathered Friends rate bags? What systems or standards do you use?
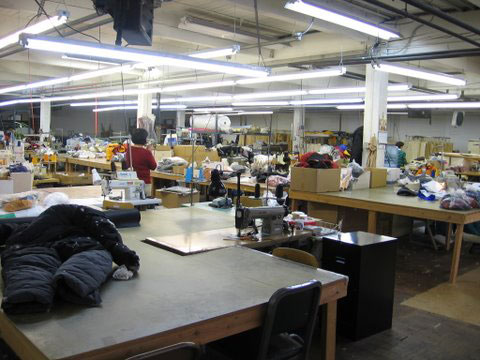
The sewing floor at Feathered Friends.
A: We rate them the same as almost every other North American manufacturer that I’m aware of still. Although some of them are starting to work with the EU standards, most use an internal rating system. So we look at the bag and we do it more by inches of loft than anything else. And then we have a correlation chart for warmth. For every inch of loft we account for another 10 degrees.
There are a few anomalies in our line because they are difficult to rate. For instance the Spoonbill, we didn’t put a rating on that because it’s almost impossible to rate something of that nature. You have two people. Is one person cold or hot? Are you both hot people?
So there is Spoonbill 5 and Spoonbill 7… five inches of loft versus seven inches of loft.
Q: How accurate are sleeping bag temps really?
A: They are generally considered comfort ratings and Feathered Friends has a reputation of being on the conservative end. You could make a sleeping bag with four inches of loft and call it a negative 60, if you wanted to, but the market will correct you really quickly.
Q: Tell us how you design a bag or make a bag. What kind of technology do you use for designing? Are we talking a cocktail napkin? Computer program/software? Pen and paper?
A: Yeah, actually, it’s not quite a napkin but you are drawing it out on paper or in your head. We don’t use a software program because again, they are really expensive. So basically it’s paper and pen.
In some respects, this is the easiest step. You can draw anything, right? But then taking it and turning it into a product is a challenge and that’s where I think some of the real artistry comes. It takes some futzing around, try it this way and that way, that didn’t work so how are we going to solve this problem.
Q: What are the tools that you're using? A sewing needle?
A: Yeah, basically, you have to take an idea it and turn it into a pattern. You don’t just cut a box and then another. Use paper to put your pattern out on, is what we do. And there are several instruments if you will, like rules and things that help you draw curves. But it’s pretty rudimentary.
Q: How do you solve issues that require choices between performance and weight?
A: There isn’t a hard fast rule there. Feathered Friends focuses on the upper end of the market so we try to find both of those, performance and weight. The third leg of that stool is generally cost. And while we bear that in mind, it’s not a huge driver. We are more focused on the higher end of things rather than the cost.
Q: How do you get the down into all those baffles?
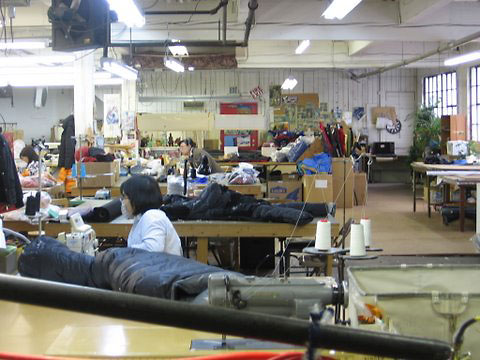
The closing station, where items that have been filled with down are sewn shut.
A: In a sleeping bag, it’s blown in with what basically looks like a vacuum. So one end of the vacuum sucks the down out of the box. The box is sitting on a very accurate scale. And then the other end is blowing it into the sleeping bag. Pretty low tech! It’s pretty fun.
Q: Do you personally test the bags you design?
A: I try to test as much as I can. I don’t get out as much as I used to or maybe as much as I’d like. We have a team of athletes who are dedicated Feathered Friends people and we’ll send stuff out with them to get their feedback. We have a number of avenues for testing before we put something on the market.
Q: Any best or worst experiences while out testing a bag?
A: Boy, well I’d say one of my best experiences is not a bag, it’s related to one of the jackets we came out with called the Jackorak.
We were up on Rainier and it’s designed to be a super lightweight windbreaker, light water resistance. When you’re testing, you take your own item in addition to something you’re testing anyway, because you’re not sure if it’s gonna work and you don’t want to put yourself in a bad, bad, bad situation. Or, you just go for it and say, we’ll go to plan B and figure out that plan once we get there.
That’s what we had done this time and we took it out and it was amazing. It blocked the wind perfect, it kept the water off, and it was a great, great experience for sure!
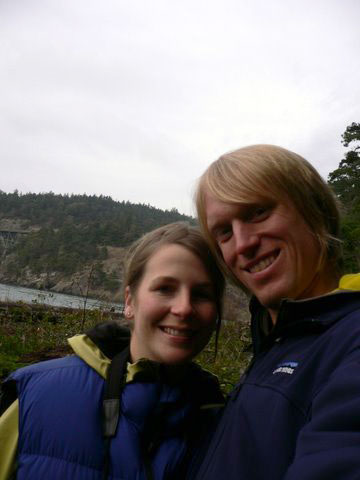
Zwiers with wife Katie at Deception Pass, Washington.
Q: You must have a worst experience or what could have been the worst if you didn’t have a Plan B?
A: Yeah, I’d say one of the not so fun experiences was last year when we were working on the Spoonbill and testing it out. We hadn’t put a zipper on the side yet, and we hadn’t figured out how to get it quite warm enough yet.
So my wife and I were holding this thing over us and we were freezin’ ass cold because it didn’t have enough loft in it and there was no zipper, so anytime someone had to get out of the bag, the other person was completely disturbed. So you had to, like, crawl out of the bag basically kicking the other person and the same thing getting back in! It wasn’t the most pleasant evening, but we made it through.
Q: Sounds like your wife loves you very much.
A: Well, so far!
Q: Have you ever nailed it on the first time with a product creation?
A: When it comes to down, it’s almost impossible to nail it the first time. How do you get the fill right? That’s one of the hardest things when dealing with down, making sure the fill is just dead on and meets your needs in terms of warmth and weight.
So when you're messing with down, you can make a jacket fifteen times to make sure you get that fill tweaked just the way you want. Now we’re talking about a difference of a few grams, not talking about being ounces away. That’s the type of accuracy and sophistication that we strive for.
Q: Which design are you most proud of? Why?
A: As far as garments are concerned, we just came out with a Daybreak Jacket for men, like a down sweater. Even more exciting, this fall we are going to have the Daybreak Jacket for woman. This is the first time Feathered Friends has done anything in garments specifically for woman. So we are working to make sure we get the fit right on the first time, so if we roll out more women’s jackets, we have it kind of dialed in.
Q: Where do you go to test bags?
A: Pretty much here in the Northwest. It’s an amazing testing ground because there are so many different applications you can put yourself in. On the western side of the crest, you can test in wet colder conditions; you can get up in the mountains and get snow and all types of temperature ranges. You can go to the east side of the crest and get a drier environment. If we need to test in applications beyond that, we always have staff traveling.
Q: What would you tell ordinary hikers and campers to do in order to get the most out of their bags?
A: Look at the fit, that’s by far the most overlooked thing by customer in terms of sleeping bags. People don’t think about their sleeping bags as having a fit and it’s probably the most important thing as far as how it will affect your experience in terms of warmth and weight.
The analogy I use a lot is, if you use a space heater in your bathroom it works really well, but if you move it to the living room, it doesn’t work as well. So think of your body as the space heater and your bag as the room. The more appropriately sized the bag is to your body, the more efficient the thermal dynamics will be. That’s one of the reasons why we have so many different cuts of our sleeping bags.
Q: Aside from testing, have you ever been cold in a bag?
A: Right after college I went to Alaska for a two-week backpacking trip and I knew some stuff based on my experiences as a child but I was way out of my league there. I didn’t have the right sleeping bag or sleeping pad, my boots didn’t fit, and I was wearing cotton head to toe. I was too poor to buy a backpack so I had an external frame women’s pack. So I learned all around a lot from a negative standpoint, but that was the coldest experience I’ve ever had.
Q: What’s the oddest question or request you have gotten?
A: The oddest thing that I’ve ever had happen was a phone call we got. Our name is unique, Feathered Friends, so if you didn’t know what we were doing and just looked us up in the phone book, you might assume that we do things other than what we do. Such as a bird store! So the oddest call was from a gentleman who sounded like he was a little bit older and he wanted to know if we had any female canaries.
Q: What’s the general feedback from customers?
A: We get tons of feedback. People generally love our stuff. Every now and then you get somebody who wants something kind of odd. One of the great things about being a manufactured-to-order company is that we can generally accommodate people’s requests. So if somebody has an idea or a design, or they want an extra pocket here or they want this extra foot, we are able to accommodate that stuff.
Obviously it comes with a price and the price is not insignificant. But we have that capacity. We’ve had people bring in sleeping bags from back in the seventies when the company first started, and the bag is still in fantastic shape. That’s the beauty of down, the lifespan and longevity as long as it’s treated properly is amazing. We also sell down by the ounce if you want to make your own down thing.
Q: What is the craziest or most bizarre design request?
A: Well, you know, we have some people who have what I would consider some odd requests, but to them it’s the greatest thing. We’ve made sleeping bags for a guy, it’s the smallest thing in the universe. I would look at it and think I could only get one leg in there, but he fits his full body inside of it. It’s an uber, uber crazy ridiculous lightweight thing. But it’s not for everybody, you know.
Q: How many bags are you producing or selling on average in a year?
A: Basically, what we manufacture is what we sell and in a given year we manufacture somewhere between 1,000 and 1,500 sleeping bags.
Q: How many new bag designs come out per year?
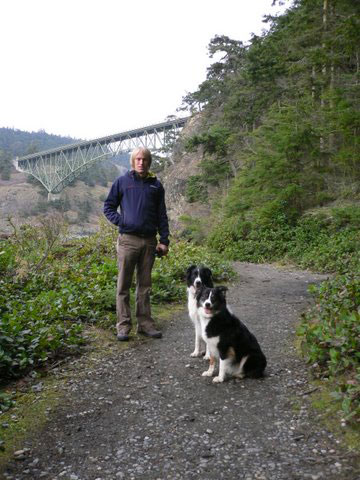
Zwiers and his Australian shepherds at Deception Pass, Washington.
A: Less than one. We make minor changes, but as far as a brand new bag, we’ve come out with three maybe four unique designs in the last fifteen years.
Q: What’s the next new unique design?
A: We are currently testing a new unique design and if the testing goes positively and works out, we could see that in about a year!
Q: Is that your brainchild?
A: Yes, absolutely.
Q: Any other hints you can give us about it?
A: No! That’s the whole show because if it doesn’t work, you know… I’m optimistic because we’ve gotten it to prototype and testing phase and usually by that time, you are eighty percent of the way there, but anything can happen.
Q: What’s the number of staff at Feathered Friends?
A: In our retail store and sales aspect we have about fifteen. In our production staff, there is another twenty-five to thirty.
Q: What are your other hobbies?
A: Besides what I do in the outdoors, which is climbing, ice climbing, skiing, biking, well I really love cooking. I enjoy gardening, and I love training my two dogs.
Q: What kind of dogs?
Australian shepherds.
(All images courtesy and copyright of Brent Zwiers and Feathered Friends.)